As we all know, the traditional linear motion is mostly through a certain transmission transformation mechanism into a linear movement of the rotation, the middle of a variety of transmission links, so the positioning accuracy of the system must take into account the accuracy of rotating motion, transmission mechanism accuracy, installation error , system wear and other factors that affect the accuracy of the system. At present, the international and domestic solutions adopt high-speed direct-drive linear motors. The mid- and low-end precision grinding screws, low-elastic deformation belts, and high-precision racks are used to minimize the accuracy of the system's transmission links. loss.
High-end direct-drive linear motors have high performances such as high speed, high acceleration, high positioning accuracy, no backlash, and other conventional transmission linear motions, but the core technologies of linear motor systems are basically controlled and controlled by developed countries. Although several domestic companies have also started to use linear motors, most of them are just motor bodies. The displacement sensors and servo controllers still need to be imported. Therefore, the overall price of the linear motor system is still high, making it truly a product that the high-end dare not dare to use. Coupled with the national strategic control of rare earth, linear motor body has slowly lost its price advantage. The price of the entire system has gradually increased. It is precisely because of the high prices that many core components need to be imported, which causes a large gap between the consumption of the entire market and traditional servo products and the overall situation is weak.
In order to fundamentally solve the problem of large-scale promotion of linear motor systems, we must start from three aspects: First, the design of the province of rare earth materials linear motor, which requires the linear motor manufacturers have advanced design tools and innovative design ideas blindly The copy of the copy of foreign countries, at most only to make a difference in the cost of labor; Second, the localization of high-performance displacement sensors, only their own master the core technology, in order to break the monopoly of international manufacturers, in order to design cost-effective products in line with China's national conditions; The third is the localization of servo controllers. Actually, there are many inverter manufacturers in China, and it is relatively easy to convert from frequency conversion to servo. However, the software algorithm is the key to measuring the performance of the entire servo controller. Almost the same. Therefore, the basic research and in-depth absorption of the algorithm is the first problem to be solved in domestic servo controllers.
Most of the middle and low end adopts the transmission mode to realize the conversion from the rotation to the current movement. The traditional way of thinking is to add an encoder to the rear end of the rotary servo motor, and then to minimize the loss of precision in the drive link through various means. Therefore, various precision screw mechanisms, precision belts, precision racks, and other high-precision drive mechanisms have been introduced to meet the needs of equipment. The goal is to allow the entire system to achieve predictable system accuracy. However, in fact, the semi-closed-loop transmission system can't meet the expected requirements because the wear of the contact drive, the looseness of the system assembly, and the deformation of the stress during the use process are increasing. Degraded use. The reason is that the system is only semi-closed, and the actual situation of the final load motion can only be estimated by the precision of the transmission mechanism. High-precision screw rods, racks, belts, etc. are difficult to process due to high processing costs, such as THK and IKO's micron screw movement is a few thousand, but also strategic control. In order to get rid of this dilemma completely, we must consider the overall system from a completely new perspective, such as how to achieve full-closed system, so that the error level of the system can not only be predicted, but can be accurately measured. The second one is how to upgrade the traditional system with lower costs, without making major changes to the original system, and achieving high-precision of the traditional drive system by adding a limited number of components.
We all know that the digital display of the machine tool is a closed-loop display that can realize displacement only by adding a grating digital display, which greatly improves the performance of traditional manual machine tools. Making machining accuracy is no longer just an expectation, it can be measured more accurately. The company's linear drive full-closed-loop solution is similar to this, there are low-end full-closed digital display solutions, but also in the high-end full-closed-loop digital solutions. This is due to our mastery of linear coding core technology and in-depth study of system replenishment control algorithms.
The full closed-loop high-precision solution not only applies to the performance upgrade of traditional servo systems, but also applies to the performance upgrade of traditional open-loop stepping slide systems. It is a middle zone to fill the traditional servo motor system and open loop stepper motor system. It is a low-cost, cost-effective and unique servo control solution. The stepping system of this solution inherits all the advantages of the traditional stepping system (for example: static lock force, good low speed performance, large torque (for the same frame type relative to the servo motor), and no response to the position loop. Time, cheap, and maintenance-free. It also has some advantages of the servo system (for example: good safety, no loss of step and overshoot, communication with the host computer, faster acceleration or deceleration, and high positioning accuracy). The stepping motor of this solution is not comparable to traditional servo motors in terms of high-speed performance and overload performance. Other performances are comparable to servo motors, and even some have better performance than servo motors (for example, static lock force, and the use of common linear scales. Higher and more reliable positioning accuracy, low speed stability, and low gear speed can be achieved without the gear box. Because this solution is very cost-effective, it will provide a more choice for industrial automation design and users, especially the economical CNC machine tool industry.
The solution is simple in principle and easy to debug. Anyone can set it up very well by using the manual. No professional commissioning technology is needed. There is no difference between the control and use and the traditional open-loop stepper motor system. Any stepper motor system can be upgraded according to this solution. After extensive use by customers, it can fully adapt to three-axis or multi-axis CNC machine tools.
This solution can work with a 0.001mm resolution grating. Fully designed for multi-axis linkage, the response to position error is microseconds, the static accuracy is a positive and negative one pulse of the grating, and the dynamic accuracy is plus or minus 2-3 pulses of the grating. The actual test on the wire cutting machine can only reach the accuracy of 0.003mm, and the circle can reach the accuracy of 0.005mm. For the machine using this solution, whether it is using a C7 screw or a C3 screw, the final machining accuracy is not much different, but the difference between the C7 and C3 screw is huge. , which is very economical.
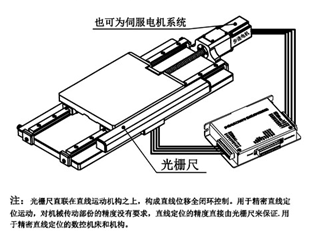
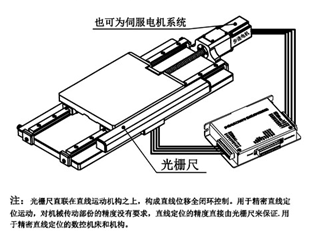